A new renaissance in U.S. manufacturing: Will Indiana miss it?
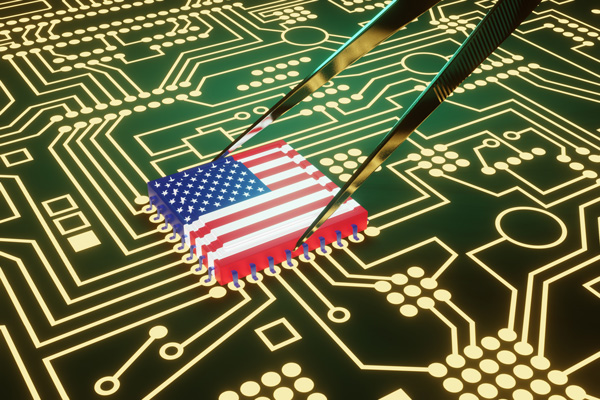
Since May of 2010, manufacturing employment in Indiana has grown 20.7% versus 13.0% nationally. While manufacturing in Indiana remains a major source of job creation when compared to national trends, it lags as a driver of higher productivity.
Trends suggest a national economic renaissance in manufacturing. Manufacturing as a percent of gross domestic product (GDP) fell from 13.1% to 10.5% between 2005 and 2020, but then reversed course and rose to 11.1% by the end of 2022.1 Manufacturing employment fell from a peak of 19.5 million in 1979 to a low of 11.5 million in 2010, but then steadily rose to nearly 13.0 million in 2023.2 Real labor productivity in manufacturing increased 11.0% between 2012 and 2022, which was better than the 9.4% gain over the same period for the economy as a whole.3,4,5,6,7 The decline of manufacturing has reversed itself in the United States – it claims a rising share of economic activity, employs an increasing number of workers and leads productivity gains in the economy.
Indiana’s uncompetitive manufacturing workforce
Among all states, manufacturing as a share of state GDP is highest in Indiana at 25.7% as of 2022.8,9,10 Since May of 2010, manufacturing employment in Indiana has grown 20.7% versus 13.0% nationally.11 While manufacturing in Indiana remains a major source of job creation when compared to national trends, it lags as a driver of higher productivity. Real labor productivity in Indiana manufacturing increased only 3.1% between 2012 and 2022, less than a third of the pace in U.S. manufacturing.12,13 Compared to other states, Indiana’s manufacturing economy is large but not innovative. Weaknesses in human capital prevent dynamism in Indiana manufacturing.
Manufacturing wages in Indiana lag the nation and Indiana is falling further behind other states. In May 2023, hourly earnings in Indiana manufacturing were 7.3% below the national average, more than double the 3.2% deficit witnessed ten years previously in May 2013.14,15 A state ranking of ninth-worst for bachelor’s degree achievement and tenth-worst for public health reflect the challenges Indiana faces in making its manufacturing workforce nationally competitive.16,17
Manufacturing steadily left the United States after 1979 in search of lower labor costs. This exit hastened a more services-based economy and forced many communities to shift away from factories as their chief source of employment and income generation. Jobs that paid good wages for workers with just a high school diploma disappeared. The median real hourly wage for a worker with no postsecondary training fell 11.1% between 1979 and 2019.18 Economic recovery was hardest for medium-sized cities extraordinarily dependent upon manufacturing with no high-wage service industries that attracted and retained college graduates. Kokomo, Anderson and Hammond were Indiana communities that fit this profile.19
Companies deciding where to locate a new plant will logically consider Indiana early because of its strong legacy in manufacturing. Consideration will only become an investment, though, if adequately skilled talent exists to fill the jobs that are created.
A return of manufacturing presents opportunity for regions once abandoned by it. Twentieth-century factory clusters shaped economic networks, infrastructure and mindsets that still make these communities advantageous for new manufacturing investment. Unlike in the past, though, talent can be a limiting factor. The labor intensity of old manufacturing made employment easy because of the repetitive manual nature of the work. In contrast, new manufacturing is capital intensive. Processes that leverage automation, advanced engineering and artificial intelligence require workers with training beyond a high school diploma. Companies deciding where to locate a new plant will logically consider Indiana early because of its strong legacy in manufacturing. Consideration will only become an investment, though, if adequately skilled talent exists to fill the jobs that are created. Indiana must quickly close educational and training gaps to avoid losing resurgent opportunities in manufacturing to other states.
A national resurgence in manufacturing
Reshoring is a new strategy among many manufacturers. Production that once moved abroad is returning to the United States. Capital investments which automatically went to foreign locations a decade ago now stay within the country. Global disruption induced by the pandemic accelerated a geographic shift that was already underway. The convergence of several macroeconomic phenomena explains why reshoring has become a rational choice for many companies.
The global labor cost advantage enjoyed by emerging economies like China and India is weaker. Economic growth in those countries increased domestic demand for talent and the domestic wages paid for it. Productivity gains proportionally lagged any rise in labor expense. This naturally made foreign workers less attractive to U.S. companies. Higher tariffs on U.S. imports, depreciation of the dollar and stronger social accountability for labor practices abroad further eroded profits from offshoring. Investment by states in better alignment of educational and training investments with regional workforce needs further encouraged consideration of reshoring options.
The rate of return on fixed assets located in the United States rose while the cost advantage of foreign talent fell. Breakthroughs in production technology dramatically increased the attractiveness of capital-intensive manufacturing. Corporate tax changes motivated repatriation of profits held abroad by U.S. companies. This unlocked funds for investment in stateside plants and equipment. The CHIPS and Science Act of 2022 and Bipartisan Infrastructure Law subsidized capital expenditures that expanded manufacturing in high economic value industries such as semiconductors, nanotechnology, clean energy and quantum computing.20 New factory designs significantly increased labor productivity and made it easier to financially justify the higher wages of U.S. workers.
New logistical challenges further strengthened the incentives for reshoring. Global supply chains became harder to manage and sustain, especially in industries that had normalized just-in-time and zero-inventory practices. Transportation strikes and public health lockdowns more frequently interrupted the international flow of goods. Tariff escalation, tighter travel requirements and new nationalistic biases in economic policy made borders harder to cross and logistics more expensive. Geopolitical tension increased the vulnerability of shipping lanes, especially in the Black Sea, Persian Gulf and South China Sea. Oil prices rose and became harder to predict. Companies felt increased pressure to reduce their carbon footprint by shortening and localizing supply chains.
Maturation of emerging economies, advances in production technology and deglobalization of markets have increased incentives for U.S. companies to base more production at home rather than abroad. These are long-term shifts that will not quickly reverse themselves.
Maturation of emerging economies, advances in production technology and deglobalization of markets have increased incentives for U.S. companies to base more production at home rather than abroad. These are long-term shifts that will not quickly reverse themselves. The opportunity for U.S. manufacturing is unprecedented, but policymakers must understand that the labor-intensive factories which left in the twentieth century are being replaced by capital-intensive factories that require small sets of skilled workers rather than large sets of unskilled workers. States that cannot supply the skilled talent will not enjoy the benefits of a new renaissance in U.S. manufacturing.
Options for Indiana’s manufacturing workforce
Before the pandemic accelerated investment in reshoring, the State of Indiana recognized and acted to close its manufacturing workforce productivity gap. Consolidation of regional community colleges into one statewide Ivy Tech system in 2005 and organization of the Governor’s Workforce Cabinet in 2018 improved capacity to implement smart workforce policies. Employer training grants, automatic enrollment of high school seniors in the 21st Century Scholars Program, off-campus career training for grades ten through twelve and regional quality of life improvement initiatives to retain talent represent recent efforts by state government to make the Indiana workforce more competitive.
While recent legislative efforts give Indiana momentum in improving manufacturing workforce productivity, there remains a question of sufficiency. Talent has been an economic priority for state government since the Department of Workforce Development was founded in 1991. Since then, though, the productivity and average wage paid an Indiana factory worker has proportionally fallen further behind the national average.
While recent legislative efforts give Indiana momentum in improving manufacturing workforce productivity, there remains a question of sufficiency.
Workforce policy must achieve three outcomes to maximize Indiana’s ability to take economic advantage of reshoring. First, well-anchored talent pipelines must move skilled graduates into manufacturing industries that make Indiana regions globally competitive. Curricula, degrees and training programs must unambiguously align with local talent needs. Second, school districts must dramatically expand learning in science, technology, engineering and mathematics (STEM). STEM skills are in highest demand and are the foundation of the highest-paying jobs in manufacturing. Third, opportunities must motivate graduates from Indiana colleges and universities to remain in the state. Indiana institutions excel in attracting students from outside of the state. Retaining these students as graduates in the Indiana workforce is an easy way to raise productivity.
With focus and strategically placed assistance from state government, Indiana can lift the value of its manufacturing workforce. Work to achieve this, though, got a late start. As reshoring accelerates, Indiana must overcome workforce disadvantages to win new factories. Positioning the state to compete in a better and determined way will allow Indiana to reclaim national leadership in manufacturing.
Notes
- U.S. Bureau of Economic Analysis. 2023. Value Added by Industry: Manufacturing as a Percentage of GDP. Retrieved from Federal Reserve Economic Data. Federal Reserve Bank of St. Louis. https://fred.stlouisfed.org/series/VAPGDPMA.
- U.S. Bureau of Labor Statistics. 2023. All Employees, Manufacturing. Retrieved from Federal Reserve Economic Data. Federal Reserve Bank of St. Louis. https://fred.stlouisfed.org/series/MANEMP.
- U.S. Bureau of Economic Analysis. 2023. Real Gross Domestic Product: Manufacturing in the United States. Retrieved from Federal Reserve Economic Data. Federal Reserve Bank of St. Louis. https://fred.stlouisfed.org/series/USMANRQGSP.
- Real GDP from manufacturing was $1.91 trillion in 2012 Q4 and $2.28 trillion in 2022 Q4 measured in 2012 dollars, which implies an increase of 19.4%. Manufacturing employment was 11,957,000 in 2012 Q4 and 12,965,000 in 2022 Q4, which implies an increase of 8.4%. Real labor productivity is real GDP divided by employment, which mathematically implies that the percentage change in real labor productivity is the percentage change in real GDP minus the percentage change in employment, which is 11.0% for manufacturing.
- U.S. Bureau of Labor Statistics. 2023. All Employees, Total Nonfarm. Retrieved from Federal Reserve Economic Data. Federal Reserve Bank of St. Louis. https://fred.stlouisfed.org/series/PAYEMS.
- U.S. Bureau of Economic Analysis. 2023. Real Gross Domestic Product. Retrieved from Federal Reserve Economic Data. Federal Reserve Bank of St. Louis. https://fred.stlouisfed.org/series/GDPC1.
- Total nonfarm real GDP was $16.30 trillion in 2012 Q4 and $20.18 trillion in 2022 Q4 measured in 2012 dollars, which implies an increase of 23.8%. Total employment was 134,860,000 in 2012 Q4 and 154,279,000 in 2022 Q4, which implies an increase of 14.4%. Real labor productivity is real GDP divided by employment, which mathematically implies that the percentage change in real labor productivity is the percentage change in real GDP minus the percentage change in employment, which is 9.4% for all sectors of the U.S. economy.
- National Association of Manufacturers. 2019. Manufacturing’s Share of Gross State Product. https://www.nam.org/wp-content/uploads/2019/05/MFG-GSP-FactSheet_201810.pdf.
- U.S. Bureau of Economic Analysis. 2023. Regional GDP and Personal Income. Interactive Data Tables. Annual Gross Domestic Product (GDP) by State, GDP in Current Dollars. https://www.bea.gov/itable/regional-gdp-and-personal-income.
- Total 2022 Indiana GDP was $455.8 billion and manufacturing’s contribution to this was $117.1 billion, or 25.7% of the state total.
- U.S. Bureau of Labor Statistics. 2023. All Employees, Manufacturing in Indiana. Retrieved from Federal Reserve Economic Data. Federal Reserve Bank of St. Louis. https://fred.stlouisfed.org/series/INMFG.
- U.S. Bureau of Economic Analysis. 2023. Regional GDP and Personal Income. Interactive Data Tables. Quarterly Gross Domestic Product (GDP) by State, Real GDP in Chained Dollars. https://www.bea.gov/itable/regional-gdp-and-personal-income.
- Real GDP from manufacturing in Indiana was $82.03 billion in 2012 Q4 and $94.86 billion in 2022 Q4 measured in chained 2012 dollars, which implies an increase of 15.6%. Manufacturing employment in Indiana was 484,900 in 2012 Q4 and 545,400 in 2022 Q4, which implies an increase of 12.5%. Real labor productivity is real GDP divided by employment, which mathematically implies that the percentage change in real labor productivity is the percentage change in real GDP minus the percentage change in employment, which is 3.1% for manufacturing in Indiana.
- U.S. Bureau of Labor Statistics. 2023. Average Hourly Earnings of All Employees: Manufacturing in Indiana. Retrieved from Federal Reserve Economic Data. Federal Reserve Bank of St. Louis. https://fred.stlouisfed.org/series/SMU18000003000000003.
- U.S. Bureau of Labor Statistics. 2023. Average Hourly Earnings of All Employees, Manufacturing. Retrieved from Federal Reserve Economic Data. Federal Reserve Bank of St. Louis. https://fred.stlouisfed.org/series/CES3000000003.
- World Population Review. 2023. Educational Attainment by State 2023. https://worldpopulationreview.com/state-rankings/educational-attainment-by-state.
- U.S. News and World Report. 2023. Public Health. Best States Rankings. https://www.usnews.com/news/best-states/rankings/health-care/public-health.
- Congressional Research Service. 2020. Real Wage Trends, 1979 to 2019. Report R45090. Washington, DC. https://sgp.fas.org/crs/misc/R45090.pdf.
- Berube, Alan and Cecile Murray. 2018. Renewing America’s Economic Promise through Older Industrial Cities. The Brookings Institution. https://www.brookings.edu/wp-content/uploads/2018/04/2018-04_brookings-metro_older-industrial-cities_full-report-berube_murray_-final-version_af4-18.pdf.
- The White House. 2022. FACT SHEET: CHIPS and Science Act Will Lower Costs, Create Jobs, Strengthen Supply Chains, and Counter China. Washington, DC. https://www.whitehouse.gov/briefing-room/statements-releases/2022/08/09/fact-sheet-chips-and-science-act-will-lower-costs-create-jobs-strengthen-supply-chains-and-counter-china/.